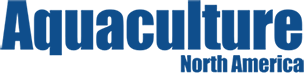
Keeping up with a changing industry
June 2, 2021
By Jennifer Brown
As fish farming expands, training becomes mission-critical

With rapid expansion and innovation in the aquaculture industry, the need for skilled employees is constant as companies try to keep up with the pace of change and the need to have front-line staff educated on how to troubleshoot systems and understand best practices.
Having a robust training program can improve quality and efficiencies at fish farm locations and improve employee engagement and retention, especially as competition for talent increases. While colleges and universities provide good foundation programs, human resource managers in the industry say the need for continuous learning is critical in an industry where the adoption of new systems, standards and certifications is constant.
The aquaculture industry is one of Canada’s smallest agricultural players, but it is the fastest-growing. It’s estimated that by 2025 there will be growing labour shortages in the industry, with 1,300 jobs predicted to go unfilled in Canada alone compared to an estimated 450 jobs unfilled in 2014, according to a report from Canadian Agriculture Human Resource Council. The demand for workers in the sector is expected to rise by an average of 2.6 per cent per year over the next five years.
Providing aquaculture employees with the right training opportunities can come in different ways, such as through in-house scheduled training with outside providers, vendor-led technology training and consulting groups who specialize in the aquaculture sector.
While the pandemic has enabled some online training opportunities not previously used before, the reality is that hands-on site-based training remains crucial in aquaculture, especially with the growth of recirculating aquaculture system (RAS) facilities.

Safety training at Mowi Canada West. Training demonstrates the company is investing in the staff’s future Photo: Mowi
Training for the human experience
The engineering and design of a new product or technology are typically based on sound scientific principles but those principles are not always passed on to the operators so they can understand what they need to do to get the best result from a system, says Melissa Rommens, vice-president of Sustain Aqua in Emyvale, Prince Edward Island.
“New technologies are coming online all the time, and there are some technologies where the supplier provides ample training, but sometimes that doesn’t happen, so there can be a gap,” says Rommens.
Sustain Aqua works with fish farmers in several areas, including training in fish handling, biosecurity, water quality management and control, solids control in RAS and water supply disinfection.
“One of the gaps where we have provided training is with the startup up of recirculating aquaculture systems. We have some great engineers in the industry and great designs, but sometimes there is a gap between the engineer and the operation,” she says.
Rommens has also assisted in attaining sustainability or organic certifications or improving management practices at a farm.
“What we have seen is the company may already have the procedures in place to meet the standards, they just have to understand how it all fits together, and maybe there is some tweaking here and there that has to be done,” she says.
Vendor-based approach
Much like most tech companies these days, increasingly, vendors in the aquaculture sector provide training with the purchase of a system. AquaMaof Group, based in Poland, has a global training center that serves to train customers on its technology. With so few people having RAS experience, the company decided in 2017 to launch the training program at its centre where customers can experience a combination of practical and theoretical training. It covers technical and managerial issues and is adapted to the specific requirements of the customer’s project and the range of skills needed at their facility. They will also provide technology updates on new system features in a shorter format.
“The technology contract we sign with our customers usually includes a basic custom training and a first-year service and support component,” says Guy Alon, customer operation and service manager at AquaMaof. “This covers both practical and theoretical training on the operation and management of AquaMaof’s RAS technology, together with in-depth training on the various components of AquaMaof’s technology as well as other important elements, such as electrical and mechanical systems, redundancy systems, water chemistry management, fish health and welfare management, and preparation for audits including for the Aquaculture Stewardship Council and Best Aquaculture Practices certification.”
With a growing demand for skilled personnel with RAS experience, Alon says he can see more institutions, including those in the academic world, create RAS training platforms. They have started to reach out to establish relationships with those organizations.
In-house approach
Company-provided training checks several boxes for organizations with the resources to set up and track continuous learning opportunities and make sure staff are up to date on the latest developments. It also demonstrates the company is investing in their future.
At Cermaq, the company supports the development of employees through in-house or third-party training opportunities. They provide on-the-job learning opportunities for fish handling and husbandry training, standard practices and day-to-day responsibilities.
They also provide specific training for employees who will be adopting new technology as part of their roles, such as on the operation of the company’s new delousers or new semi-closed containment systems.
“Many of our technology investments are purchased with the caveat that the manufacturer provides employee training as part of the purchase,” says Amy Jonsson, communications and engagement manager at Cermaq.
“We believe in developing our employees and promoting internally,” says Jonsson. “To do this, we support both formal and informal ongoing learning for employees and provide job sharing, mentorship programs and leadership skill development opportunities.”
At Mowi, a four-tier technician advancement program and corresponding training program provide a clear path to employees as to how they can move up in the organization.
“It helps with retention and shows our employees we’re invested in them and gives them a higher level of engagement and pay that is attached to moving through those technician levels,” says Dean Dobrinsky, human resources director with Mowi in British Columbia.
Dobrinsky also credits local post-secondary schools such as North Island College, Excel Career College and Vancouver Island University as producing graduates that become employees in the Mowi facilities.
“They offer good foundational salmon farming training. We draw on those programs for employees, and our own internal system adds the experiential component to it as well,” he says.
As aquaculture and salmon farming is still a young industry, Dobrinsky says many of the technologies involved are still being developed and learned. Innovation is happening so fast the education side is continually catching up to advancements in the industry itself.
“We have employees who work at hatcheries who have come from programs where they have had the opportunity to learn those systems on a small scale, but salmon farming from the sea site side is a lot more challenging, so we find our advancement program is beneficial not only for employees but for us as we can help them build on their skills in a way that is real,” says Dobrinsky.
At Grieg Seafood, the company has learning partnerships with Dalhousie University in Halifax and Fleming College in Peterborough, Ontario and other schools with aquaculture programs across Canada.
“We’re open to any partnership that would add value to the training opportunities we offer,” says Mihaela Ciocan, human resource generalist at Grieg Seafood in Campbell River, B.C.
“COVID-19 has restricted training in some respects — my preference is to have staff join a class, but we always want to make sure training is happening safely,” she says. “Everything we have been able to move online we have — most training providers have been flexible in finding a way to offer training in this new environment.”
Like any industry evolving to meet market demand, attracting skilled workers is critical, and helping them find the training to stay current and produce a better product faster will help organizations remain competitive.